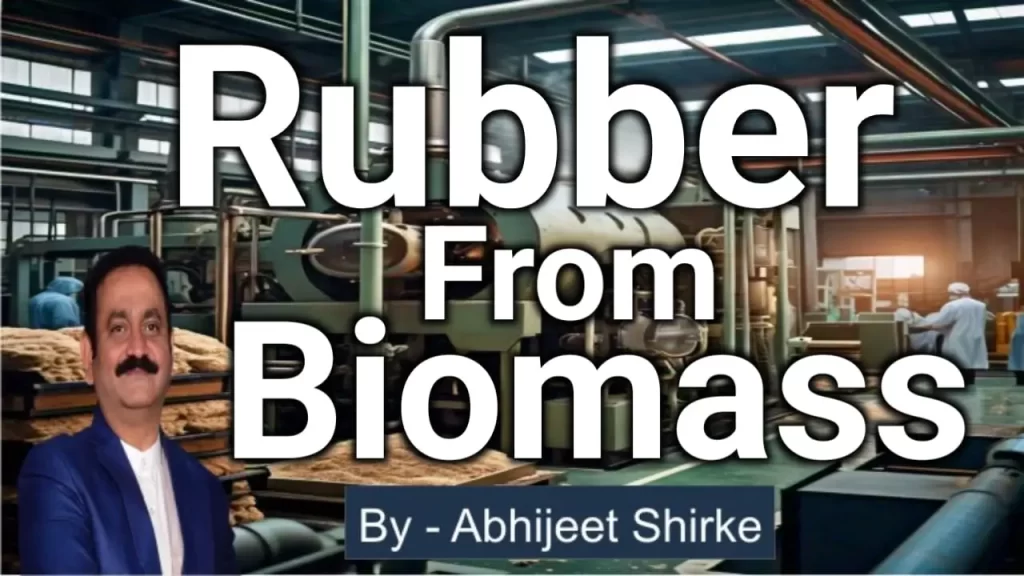
Rubber From Biomass, also known as bio-rubber, is produced through the fermentation of biomass feed stocks such as corn starch, sugarcane, or potato starch. Microorganisms like bacteria or yeast convert the biomass into a rubber-like material, which can be processed into various forms and products. The benefits of bio-rubber are numerous. It is biodegradable, non-toxic, and requires less energy to produce than traditional rubber. Additionally, bio-rubber can be designed to have specific properties, such as improved durability or elasticity, making it suitable for a wide range of applications, from tires and automotive parts to medical devices and consumer goods.
The production of rubber, a vital material for various industries, has long relied on petroleum-based sources. However, with growing concerns about sustainability and environmental impact, researchers have been exploring alternative methods for producing rubber. One promising approach is the use of biomass, renewable organic materials, to create a sustainable and eco-friendly alternative to traditional rubber.
Several companies and research institutions are already developing bio-rubber technologies, with some pilot-scale production facilities in operation. While challenges remain, such as scaling up production and reducing costs, the potential for bio-rubber to transform the rubber industry is significant.
The shift to bio-rubber could also have a positive impact on the environment. By utilizing renewable biomass sources, the dependence on fossil fuels is reduced, and greenhouse gas emissions are lowered. Furthermore, bio-rubber can be composted at the end of its life cycle, reducing waste and the environmental harm associated with traditional rubber disposal.
As the demand for sustainable materials continues to grow, bio-rubber is poised to play a vital role in the transition to a more circular and environmentally conscious economy. With ongoing research and development, bio-rubber has the potential to revolutionize the rubber industry and contribute to a more sustainable future.
1. Traditional Rubber Production from Fossil Fuels
Traditional rubber production has historically relied heavily on two primary sources: natural rubber derived from latex-producing plants, particularly the rubber tree Heveabrasiliensis, and synthetic rubber manufactured from fossil fuels. While natural rubber is harvested by tapping latex from trees, synthetic rubber is produced through the polymerization of petrochemical derivatives such as styrene and butadiene. This process is energy-intensive, relying on non-renewable resources, and contributes significantly to environmental degradation, including greenhouse gas emissions and pollution from petrochemical processes.
The rise of synthetic rubber in the early 20th century was driven by the demand for rubber products that could withstand extreme conditions, such as tires for automobiles and airplanes, and industrial components. Unlike natural rubber, synthetic variants offered greater resistance to wear and tear, heat, and chemicals, which made them indispensable in various industries. However, the environmental cost of this reliance on fossil fuels has become increasingly apparent.
Fossil fuel extraction, processing, and combustion have contributed to environmental challenges, including climate change, air and water pollution, and habitat destruction. The production of synthetic rubber alone accounts for a substantial portion of global greenhouse gas emissions, further exacerbating the climate crisis. Additionally, the rubber industry’s dependency on non-renewable resources has raised concerns about long-term sustainability, given the finite nature of fossil fuel reserves.
In recent years, there has been growing interest in finding sustainable alternatives to fossil fuel-based rubber. As industries and consumers alike become more environmentally conscious, the pressure to reduce carbon footprints and shift towards renewable resources has intensified. This has spurred research and development into alternative rubber sources that do not rely on petrochemicals, paving the way for innovations such as biomass-based rubber.
Biomass, derived from organic materials such as plants and agricultural waste, offers a promising pathway for producing rubber in a more sustainable and environmentally friendly manner. By tapping into renewable feed stocks, the rubber industry can reduce its dependence on fossil fuels, lower greenhouse gas emissions, and contribute to the circular economy. This shift towards biomass-based rubber represents a significant step forward in the quest for a greener and more sustainable future.
2. Biomass as a Renewable Feedstock for Rubber Production
Biomass is a versatile and renewable feedstock that encompasses a wide range of organic materials, including plant residues, agricultural by-products, forestry waste, and even algae. As the global demand for sustainable materials grows, biomass has emerged as a key player in the development of renewable alternatives to traditional petrochemical-based products, including rubber.
In the context of rubber production, biomass can be transformed into various intermediate products, such as bio-oils, bio-based monomers, and polymers, which can then be processed into rubber-like materials. The use of biomass as a feedstock offers several advantages, including renewability, reduced carbon footprint, and the potential for biodegradability. These attributes align with the increasing emphasis on sustainability and environmental responsibility in the manufacturing sector.
The diversity of biomass sources allows for flexibility in selecting the most appropriate feedstock for rubber production, depending on regional availability, cost, and specific material properties required for the end product. For instance, some biomass sources are rich in hydrocarbons, making them ideal candidates for conversion into rubber precursors. Others may contain specific compounds that can be directly polymerized or chemically modified to create rubber-like materials.
One of the most promising aspects of biomass as a feedstock is its potential to be sourced sustainably. For example, agricultural residues that would otherwise be discarded or burned can be repurposed as raw materials for rubber production. Similarly, dedicated energy crops, such as guayule and Russian dandelion, can be cultivated specifically for their latex or rubber-producing capabilities. These plants offer the added benefit of being drought-resistant and suitable for growth in marginal lands, reducing competition with food crops and minimizing environmental impact.
The transition to biomass-based rubber production is not without challenges, including the need for efficient conversion technologies, the scalability of production processes, and the economic feasibility of biomass as a competitive feedstock. However, ongoing research and innovation in biotechnology, chemical engineering, and materials science are paving the way for the development of viable pathways for producing high-quality rubber from renewable resources.
biomass presents a compelling alternative to fossil fuels for rubber production, offering the potential for a more sustainable and eco-friendly material supply chain. As industries continue to explore and invest in biomass-based technologies, the role of biomass as a renewable feedstock for rubber production is expected to grow, contributing to the broader shift towards a circular and low-carbon economy.
3. Importance of Sustainable and Biodegradable Rubber Alternatives
The growing environmental concerns associated with traditional rubber production, particularly synthetic rubber derived from fossil fuels, have underscored the need for sustainable and biodegradable alternatives. As industries and consumers alike become more conscious of their environmental impact, the demand for materials that are both eco-friendly and high-performing has intensified. In this context, sustainable and biodegradable rubber alternatives have emerged as critical components of a greener future.
One of the key drivers for the development of sustainable rubber alternatives is the urgent need to reduce greenhouse gas emissions. Traditional synthetic rubber production is energy-intensive and heavily reliant on petrochemicals, which contribute significantly to global carbon emissions. By contrast, rubber derived from renewable biomass sources offers the potential to lower carbon footprints and mitigate climate change. The use of biomass as a feedstock can sequester carbon during the growth phase of the raw materials, offsetting emissions associated with production and disposal.
In addition to reducing emissions, sustainable rubber alternatives address the issue of environmental pollution. Synthetic rubber is not biodegradable, leading to the accumulation of non-degradable waste in landfills and natural ecosystems. This has significant ecological implications, as rubber waste can persist in the environment for decades, contributing to soil and water contamination. Biodegradable rubber alternatives, on the other hand, can break down naturally over time, reducing the environmental burden of rubber waste.
The concept of a circular economy also plays a crucial role in the importance of sustainable rubber alternatives. In a circular economy, materials are reused, recycled, and regenerated to minimize waste and extend the lifecycle of products. Biomass-based rubber, which can be derived from agricultural residues or dedicated energy crops, aligns with this model by promoting the use of renewable resources and enabling the recycling of end-of-life rubber products. This not only conserves natural resources but also reduces the need for virgin material extraction, further enhancing sustainability.
Moreover, the development of sustainable rubber alternatives is essential for addressing the social and economic dimensions of sustainability. Many regions that produce natural rubber are facing challenges related to deforestation, land-use change, and social inequities. By diversifying rubber production to include sustainable and locally-sourced biomass, it is possible to reduce the pressure on natural rubber-producing regions, promote fair trade practices, and support rural economies.
The shift towards sustainable and biodegradable rubber alternatives represents a vital step in the broader movement towards sustainable development. As industries increasingly recognize the environmental, economic, and social benefits of these alternatives, the adoption of biomass-based rubber is likely to accelerate, paving the way for a more sustainable and resilient material economy.
4. Types of Biomass Suitable for Rubber Production
Biomass refers to organic materials derived from plants, animals, or microorganisms that can be used as a renewable resource for various applications, including rubber production. In the quest for sustainable alternatives to fossil fuel-based rubber, certain types of biomass have shown particular promise due to their chemical composition, renewability, and potential for large-scale cultivation. Among the most notable biomass sources for rubber production are guayule, Russian dandelion, and other plant-based materials.
Guayule (Partheniumargentatum) is a shrub native to the south western United States and northern Mexico. It has been identified as a highly promising alternative to the traditional rubber tree (Heveabrasiliensis) because it produces latex that can be used to make natural rubber. Guayule is particularly appealing because it can be grown in arid and semi-arid regions, requiring significantly less water than rubber trees. Additionally, guayule latex is hypoallergenic, making it suitable for medical and other applications where latex allergies are a concern. The entire plant can be utilized, with the latex extracted from the shrub’s stems and branches, and the remaining biomass used for bio energy or other bio products, contributing to the circular economy.
Russian dandelion (Taraxacumkok-saghyz) is another plant species that has gained attention as a potential source of natural rubber. Native to Central Asia, this dandelion species produces a milky latex in its roots that can be processed into rubber. Russian dandelion has the advantage of being able to grow in temperate climates, which could expand the geographical range of rubber production beyond tropical regions. The latex yield from Russian dandelion is comparable to that of the rubber tree, and ongoing research is focused on optimizing cultivation practices and improving the efficiency of latex extraction. Like guayule, Russian dandelion also offers the potential for the entire plant to be used, with non-latex components serving as feedstock for other bio products.
In addition to guayule and Russian dandelion, other biomass sources, such as soybeans, sugarcane, and various grasses, are being explored for their potential in rubber production. These materials can be converted into rubber-like polymers through chemical or biological processes, such as fermentation or enzymatic conversion. The diversity of biomass feed stocks offers flexibility in selecting the most appropriate source based on regional availability, cost, and desired material properties.
The development of biomass-based rubber from these sources represents a significant opportunity to reduce reliance on fossil fuels and traditional rubber trees, which are often associated with environmental concerns such as deforestation and biodiversity loss. As research and technology continue to advance, the use of these and other biomass feed stocks for rubber production is expected to play a key role in the transition to more sustainable and eco-friendly materials.
5. Conversion Processes (Pyrolysis, Gasification, etc.)
The conversion of biomass into rubber or rubber-like materials involves a series of complex processes that transform organic matter into usable polymers. These processes are crucial for unlocking the potential of biomass as a renewable feedstock for rubber production. Among the most notable conversion technologies are pyrolysis, gasification, and other biochemical and chemical processes that break down biomass into simpler compounds, which can then be reassembled into rubber materials.
Pyrolysis is a thermal decomposition process that occurs in the absence of oxygen. When biomass is subjected to high temperatures, it breaks down into a mixture of gases, liquids, and solid residues (bio char). The liquid fraction, often referred to as bio-oil, contains a variety of chemical compounds that can be further processed into bio-based monomers, which serve as the building blocks for rubber. Pyrolysis is particularly attractive for rubber production because it can handle a wide range of biomass types, from agricultural residues to woody materials. The versatility of pyrolysis, combined with its potential for producing high-value chemicals, makes it a promising pathway for converting biomass into rubber-like materials.
Gasification is another thermal process that involves the partial oxidation of biomass at high temperatures, producing a synthesis gas (syngas) composed primarily of carbon monoxide, hydrogen, and carbon dioxide. Syngas can be used as a precursor for various chemical processes, including the synthesis of monomers such as butadiene and isoprene, which are key components in synthetic rubber production. Gasification offers the advantage of producing a cleaner and more consistent product than pyrolysis, and it can be integrated with existing chemical manufacturing infrastructure to produce bio-based rubber materials.
In addition to thermal processes, biochemical conversion methods, such as microbial fermentation and enzymatic hydrolysis, play a significant role in biomass-to-rubber production. Microbial fermentation, for example, involves the use of microorganisms to convert sugars derived from biomass into rubber precursors. Certain bacteria and fungi can produce polyisoprene, the main polymer in natural rubber, through fermentation. This biological approach is particularly appealing for its lower energy requirements and potential for producing rubber with specific properties tailored to different applications.
Chemical conversion processes also contribute to the production of rubber from biomass. These methods often involve the catalytic transformation of biomass-derived intermediates into monomers or polymers suitable for rubber production. Catalysts play a crucial role in improving the efficiency and selectivity of these reactions, enabling the production of high-quality rubber materials with properties comparable to those of traditional fossil fuel-based rubber.
The choice of conversion process depends on several factors, including the type of biomass, the desired end product, and the economic feasibility of the process. Each method has its advantages and challenges, and ongoing research is focused on optimizing these processes to enhance yield, reduce costs, and minimize environmental impact.
The conversion of biomass into rubber involves a diverse array of processes, each with its own set of opportunities and challenges. By harnessing these technologies, the rubber industry can reduce its reliance on fossil fuels and move towards more sustainable and eco-friendly production methods, contributing to the broader goals of carbon neutrality and resource conservation.
6. Rubber From Biomass Production Pathways
The production of rubber from biomass involves various pathways, each characterized by distinct biological, chemical, or hybrid processes that convert organic feedstocks into rubber-like materials. These pathways leverage different technological approaches to achieve the same goal: creating sustainable and high-performance rubber that can replace conventional fossil fuel-derived rubber in various applications.
Biological production pathways utilize living organisms, such as bacteria, yeast, and plants, to produce rubber or rubber precursors. One of the most well-known biological pathways is the cultivation of rubber-producing plants like guayule and Russian dandelion, which naturally produce latex—a form of natural rubber. This latex can be harvested and processed into rubber without the need for complex chemical synthesis, making it a straightforward and eco-friendly option. However, biological pathways are not limited to plant-derived latex.
Advances in synthetic biology and metabolic engineering have enabled the development of microbial strains that can produce rubber-like polymers through fermentation. These engineered microorganisms can convert sugars or other biomass-derived feed stocks into polyisoprene, the primary polymer in natural rubber. The biological approach offers the potential for producing rubber with specific properties, such as enhanced elasticity or resistance to degradation, by tweaking the metabolic pathways of the microorganisms involved.
Chemical production pathways involve the transformation of biomass into rubber through a series of chemical reactions. These pathways often begin with the breakdown of biomass into simpler molecules, such as syngas or bio-oil, which can then be chemically converted into monomers like butadiene, isoprene, or styrene. These monomers are subsequently polymerized to form synthetic rubber. The chemical approach allows for precise control over the rubber’s composition and properties, enabling the production of specialized rubber grades for different industrial uses. For instance, bio-based butadiene can be polymerized into polybutadiene rubber, which is commonly used in tires, while bio-based isoprene can be used to produce polyisoprene rubber for medical and consumer goods.
Hybrid production pathways combine elements of both biological and chemical processes to optimize efficiency and product quality. In these pathways, biomass is first biologically converted into intermediate products, which are then chemically modified or polymerized to produce rubber. For example, a hybrid pathway might involve the fermentation of biomass-derived sugars into bio-based ethanol, followed by the catalytic conversion of ethanol into butadiene for rubber production. This approach allows for greater flexibility in feedstock selection and process optimization, making it a versatile option for scaling up biomass-to-rubber production.
Each of these production pathways has its own set of advantages and limitations. Biological pathways are often more sustainable and environmentally friendly, but they may be constrained by lower yields and longer production times. Chemical pathways offer higher efficiency and scalability but may require more energy and involve harsher processing conditions. Hybrid pathways seek to balance these trade-offs by leveraging the strengths of both approaches.
The production of rubber from biomass can be achieved through a variety of pathways, each tailored to specific feed stocks, production scales, and end-use requirements. As research and development in this field continue to advance, these pathways will become increasingly refined, enabling the production of high-quality, sustainable rubber that can meet the growing demand for eco-friendly materials in a wide range of industries.
7. Chemical Composition of Biomass-Based Rubber
The chemical composition of biomass-based rubber is a critical factor that determines its physical properties, performance characteristics, and potential applications. Understanding this composition is essential for optimizing the production processes and ensuring that biomass-based rubber can effectively replace traditional fossil fuel-derived rubber in various industrial applications.
Biomass-based rubber primarily consists of polymers that are chemically similar to those found in natural or synthetic rubber. The most common polymer in traditional rubber is polyisoprene, a polymer of the monomer isoprene. In the case of biomass-based rubber, the source of isoprene or other rubber precursors can vary, depending on the type of biomass and the conversion process used.
For instance, natural rubber derived from guayule or Russian dandelion is composed of polyisoprene, much like the latex from the rubber tree (Heveabrasiliensis). The isoprene units in polyisoprene are linked in a cis-1,4 configuration, which gives the rubber its characteristic elasticity and flexibility. The high molecular weight and cis-configuration of polyisoprene are essential for the rubber’s ability to stretch and recover, making it ideal for products like tires, medical gloves, and various elastic materials.
In synthetic biomass-based rubber, the chemical composition can be more varied. Depending on the monomers used and the polymerization process, biomass-based rubber can contain a mixture of different polymers, such as polybutadiene, polystyrene, or polyisoprene. These polymers may be derived from biomass through biochemical or chemical pathways. For example, butadiene, which is a key monomer in synthetic rubber, can be produced from bio-based ethanol or syngas obtained through the gasification of biomass. The resulting polybutadiene rubber is known for its resistance to wear and its low-temperature flexibility, making it suitable for tire manufacturing and other industrial applications.
The chemical structure of biomass-based rubber can be tailored to meet specific performance requirements by adjusting the type and ratio of monomers used in the polymerization process. For example, by incorporating styrene monomers into the polymer chain, it is possible to produce styrene-butadiene rubber (SBR), which has enhanced abrasion resistance and durability. This ability to customize the chemical composition of biomass-based rubber makes it a versatile material that can be engineered for a wide range of applications, from automotive to consumer goods.
The presence of other components in biomass, such as lignin, cellulose, and hemicellulose, can also influence the properties of the resulting rubber. While these components are typically removed or converted during the production process, their residues can sometimes remain in the final product, affecting its mechanical properties, such as strength, elasticity, and thermal stability. Research is ongoing to optimize the purification and conversion processes to minimize these effects and improve the quality of biomass-based rubber.
The chemical composition of biomass-based rubber is a key determinant of its functionality and suitability for different applications. By understanding and manipulating this composition, manufacturers can produce high-quality, sustainable rubber that meets the demands of various industries, while also reducing reliance on fossil fuels and minimizing environmental impact.
8. Comparison to Traditional Fossil Fuel-Based Rubber
Comparing biomass-based rubber to traditional fossil fuel-based rubber involves examining several key aspects, including environmental impact, performance characteristics, production processes, and economic considerations. This comparison is essential for understanding the potential of biomass-based rubber as a viable alternative to conventional rubber and for identifying areas where further innovation and development are needed.
- Environmental Impact: One of the most compelling advantages of biomass-based rubber is its significantly lower environmental footprint compared to traditional fossil fuel-based rubber. Conventional rubber production relies heavily on petrochemical feed stocks, particularly butadiene and styrene, which are derived from crude oil. The extraction, refining, and processing of these fossil fuels contribute to a high level of greenhouse gas emissions, resource depletion, and environmental pollution. In contrast, biomass-based rubber is derived from renewable sources such as guayule, dandelion, or agricultural residues. These feed stocks can be cultivated sustainably, often with lower inputs of water, pesticides, and fertilizers, reducing the overall environmental impact. Additionally, the carbon dioxide absorbed by biomass during its growth partially offsets the emissions generated during rubber production, contributing to a smaller carbon footprint.
- Performance Characteristics: In terms of performance, biomass-based rubber can be engineered to match or even exceed the properties of traditional fossil fuel-based rubber, depending on the application. For example, natural rubber from guayule has shown comparable tensile strength, elasticity, and durability to that of Hevea rubber, which is widely used in tires and other products. Moreover, by carefully selecting the biomass feedstock and optimizing the conversion processes, it is possible to produce synthetic rubber with specific characteristics, such as enhanced abrasion resistance, improved thermal stability, or increased flexibility. However, there are still challenges in achieving the same level of consistency and performance across all applications, particularly in high-performance sectors like automotive and aerospace, where the demands on material properties are exceptionally high.
- Production Processes: The production of traditional fossil fuel-based rubber involves well-established petrochemical processes that are efficient and scalable. However, these processes are energy-intensive and rely on non-renewable resources. In contrast, the production of biomass-based rubber involves a variety of biological, chemical, and hybrid pathways, each with its own set of advantages and challenges. While biomass conversion technologies like pyrolysis, gasification, and microbial fermentation are advancing rapidly, they still face hurdles in terms of scalability, process efficiency, and cost-effectiveness. For instance, the yield of rubber precursors from biomass is currently lower than that from petrochemical sources, which can make biomass-based rubber more expensive to produce on a large scale. Additionally, the need for specialized infrastructure and the variability in biomass feed stocks can complicate the production process.
- Economic Viability: The economic competitiveness of biomass-based rubber compared to traditional fossil fuel-based rubber is influenced by several factors, including the cost of feed stocks, the efficiency of conversion technologies, and market demand for sustainable products. While the cost of biomass feed stocks can be lower than that of petrochemicals, particularly in regions with abundant agricultural residues or waste biomass, the current inefficiencies in conversion processes can lead to higher production costs. However, as technologies improve and economies of scale are achieved, the cost gap between biomass-based and traditional rubber is expected to narrow. Moreover, the growing demand for eco-friendly and sustainable products, driven by consumer preferences and regulatory pressures, is likely to create a favorable market environment for biomass-based rubber, potentially offsetting the higher production costs.
while biomass-based rubber offers significant environmental benefits and the potential for comparable or superior performance in certain applications, it still faces challenges related to production efficiency and economic viability. Ongoing research and development, coupled with supportive policies and market incentives, will be crucial in overcoming these challenges and realizing the full potential of biomass-based rubber as a sustainable alternative to traditional fossil fuel-based rubber.
9. Benefits of Biomass-Based Rubber (Reduced Greenhouse Gas Emissions, etc.)
Biomass-based rubber presents a range of benefits that make it an attractive alternative to traditional fossil fuel-based rubber. These benefits span environmental, economic, and social dimensions, contributing to the sustainability of the rubber industry and its alignment with global efforts to reduce carbon emissions and mitigate climate change.
- Reduced Greenhouse Gas Emissions: One of the most significant advantages of biomass-based rubber is its potential to reduce greenhouse gas (GHG) emissions. Traditional rubber production, which relies on petrochemicals, contributes to significant carbon dioxide (CO2) emissions throughout its lifecycle—from the extraction and processing of crude oil to the manufacturing of synthetic rubber. In contrast, biomass-based rubber is derived from renewable feed stocks such as plants or agricultural residues, which absorb CO2 from the atmosphere during their growth. This natural carbon sequestration helps to offset the emissions generated during the conversion of biomass into rubber, resulting in a lower overall carbon footprint. Additionally, some biomass conversion processes, such as microbial fermentation, operate at lower temperatures and pressures than traditional petrochemical processes, further reducing energy consumption and associated emissions.
- Sustainability and Resource Efficiency: Biomass-based rubber contributes to greater sustainability by utilizing renewable resources and promoting resource efficiency. Unlike fossil fuels, which are finite and depleting, biomass feed stocks can be replenished through sustainable agricultural practices. Moreover, the use of non-food biomass, such as crop residues or dedicated energy crops, reduces competition with food production and minimizes the impact on land use. This approach supports the circular economy by converting waste materials into valuable products, reducing the need for virgin resources, and minimizing waste generation.
- Biodegradability and Reduced Environmental Impact: Many forms of biomass-based rubber, particularly those derived from natural latex, are biodegradable, meaning they can break down naturally in the environment without leaving harmful residues. This contrasts with some traditional synthetic rubbers, which can persist in the environment for decades, contributing to plastic pollution and harming ecosystems. The biodegradability of biomass-based rubber makes it especially suitable for single-use products, such as gloves or packaging materials, where environmental impact is a key concern. Furthermore, the use of bio-based additives and fillers in rubber formulations can enhance biodegradability and reduce the reliance on harmful chemicals.
- Economic and Social Benefits: The production of biomass-based rubber can stimulate economic growth and job creation in rural areas, particularly in regions where Agriculture is a primary industry. By cultivating rubber-producing plants like guayule or dandelion, farmers can diversify their income streams and reduce their dependence on traditional crops, which may be subject to price volatility or climate-related risks. Additionally, the development of biomass-based rubber industries can spur innovation and investment in green technologies, fostering a more resilient and sustainable economy. On a social level, the shift to biomass-based rubber can contribute to improved health and safety by reducing exposure to hazardous chemicals used in conventional rubber production.
- Alignment with Regulatory and Market Trends: The growing emphasis on sustainability and environmental responsibility in both regulatory frameworks and consumer preferences is driving demand for eco-friendly materials. Biomass-based rubber aligns with these trends by offering a more sustainable alternative that meets the requirements of green certifications and standards. Companies that adopt biomass-based rubber can enhance their brand reputation, meet the expectations of environmentally conscious consumers, and comply with regulations aimed at reducing carbon emissions and promoting sustainable sourcing.
Biomass-based rubber offers a wide range of benefits, including reduced greenhouse gas emissions, enhanced sustainability, biodegradability, and positive economic and social impacts. These advantages make it a promising alternative to traditional rubber, supporting the transition to a more sustainable and circular economy.
10. Challenges in Scaling Up Production (Cost, Infrastructure, etc.)
While biomass-based rubber holds significant promise as a sustainable alternative to fossil fuel-derived rubber, scaling up its production to meet industrial demand presents several challenges. These challenges are primarily related to cost, infrastructure, technological readiness, and market acceptance, all of which need to be addressed to fully realize the potential of biomass-based rubber.
- High Production Costs: One of the most significant barriers to scaling up biomass-based rubber production is the high cost associated with the conversion processes. Biomass conversion technologies, such as pyrolysis, gasification, and microbial fermentation, are often more expensive than traditional petrochemical processes. These costs arise from several factors, including the need for specialized equipment, lower yields of rubber precursors from biomass, and the complexity of processing heterogeneous feed stocks. Additionally, the cost of biomass feed stocks can vary widely depending on availability, location, and competition with other industries, such as biofuels or bioplastics. Although economies of scale could eventually reduce these costs, significant investment in research and development is required to improve process efficiency and make biomass-based rubber economically competitive with traditional rubber.
- Infrastructure Requirements: Scaling up biomass-based rubber production requires substantial infrastructure investments. This includes the development of facilities for biomass cultivation, harvesting, and processing, as well as the construction of conversion plants capable of handling large volumes of biomass feed stocks. In regions where the necessary infrastructure is lacking, the initial capital investment can be a significant hurdle. Moreover, the transportation and logistics involved in sourcing and delivering biomass to conversion facilities can add to the overall cost and complexity of production. Ensuring a reliable and consistent supply of biomass feed stocks is also critical, as fluctuations in availability or quality can disrupt production and affect the final product’s performance.
- Technological Challenges: While advances in biomass conversion technologies have been significant, several technical challenges remain in scaling up production. For example, improving the yield and selectivity of conversion processes is essential to maximize the output of rubber precursors and reduce waste. Additionally, the variability of biomass feed stocks—due to differences in plant species, growth conditions, and seasonal availability—can impact the efficiency and consistency of conversion processes. Developing robust and flexible technologies that can accommodate a wide range of feed stocks is crucial for large-scale production. Furthermore, the integration of new technologies with existing industrial systems presents another challenge, as retrofitting or replacing established petrochemical infrastructure can be costly and time-consuming.
- Market Acceptance and Demand: The successful commercialization of biomass-based rubber also depends on market acceptance and demand. While there is growing interestin sustainable materials, the market for biomass-based rubber is still in its early stages. One of the key challenges is convincing manufacturers and consumers to switch from traditional fossil fuel-based rubber to biomass-based alternatives. This requires demonstrating that biomass-based rubber can meet or exceed the performance characteristics of conventional rubber in terms of durability, elasticity, and resistance to wear and tear. Additionally, the higher costs associated with biomass-based rubber may deter some manufacturers, particularly if the economic benefits are not immediately clear.
To drive market acceptance, it is crucial to educate stakeholders—ranging from manufacturers to end consumers—about the environmental and social benefits of biomass-based rubber. Clear communication about the sustainability of biomass sources, the reduction in greenhouse gas emissions, and the potential for biodegradability can help build demand. Furthermore, the development of industry standards and certifications for biomass-based rubber can provide assurance of quality and sustainability, making it easier for manufacturers to adopt these materials.
- Policy and Regulatory Support: Governments and regulatory bodies play a significant role in facilitating the scale-up of biomass-based rubber production. Policies that support renewable energy and sustainable materials can help offset the higher costs of production and encourage investment in infrastructure and technology. For instance, tax incentives, subsidies, or grants for research and development in biomass conversion technologies can accelerate innovation and reduce production costs. Additionally, regulations that mandate the use of sustainable materials in certain industries, such as automotive or packaging, can create a stable demand for biomass-based rubber.
- Supply Chain and Sourcing Challenges: Establishing a reliable and sustainable supply chain for biomass feed stocks is another critical challenge. The availability and quality of biomass can be affected by various factors, including climate conditions, agricultural practices, and competition with other uses. Ensuring that biomass is sourced sustainably, without causing deforestation, land degradation, or negative impacts on food security, is essential for the long-term viability of biomass-based rubber. Moreover, the global supply chain for biomass-based rubber needs to be developed to ensure that feed stocks can be efficiently transported and processed into rubber at an industrial scale.
- Innovation and Collaboration: Overcoming the challenges associated with scaling up biomass-based rubber production will require innovation and collaboration across the industry. This includes partnerships between academia, industry, and government to advance research and development, as well as collaborations between manufacturers and suppliers to create integrated supply chains. Public-private partnerships can also play a crucial role in addressing infrastructure and technological challenges, ensuring that biomass-based rubber can be produced at scale in a cost-effective and sustainable manner.
while there are significant challenges to scaling up biomass-based rubber production, these can be addressed through a combination of technological innovation, infrastructure development, market education, and supportive policies. By overcoming these barriers, biomass-based rubber can become a viable and sustainable alternative to traditional rubber, contributing to a more circular and low-carbon economy.
11. Certification and Standards for Sustainable Rubber
As the demand for sustainable materials grows, the need for robust certification and standards for biomass-based rubber becomes increasingly important. Certification and standards play a critical role in ensuring that biomass-based rubber is produced in a way that meets environmental, social, and economic sustainability criteria. They provide transparency and accountability throughout the supply chain, helping manufacturers and consumers make informed choices and fostering trust in sustainable rubber products.
- The Role of Certification: Certification schemes are designed to verify that rubber production practices adhere to specific sustainability criteria, which can include responsible sourcing of biomass feed stocks, minimizing environmental impact, and ensuring fair labor practices. These schemes often involve third-party audits and assessments to ensure compliance with established standards. Certification provides a credible way for manufacturers to demonstrate their commitment to sustainability, differentiate their products in the market, and meet the growing demand for eco-friendly materials.
One of the key certification programs relevant to sustainable rubber is the Forest Stewardship Council (FSC) certification, which ensures that rubber is sourced from responsibly managed forests that provide environmental, social, and economic benefits. While FSC certification is traditionally associated with wood products, it can also apply to rubber production, particularly when rubber is sourced from forests or plantations. Another relevant certification is the Global Organic Textile Standard (GOTS), which covers the production of organic rubber, ensuring that it is free from harmful chemicals and produced in an environmentally and socially responsible manner.
- Development of Standards: In addition to certification programs, the development of industry standards is crucial for the widespread adoption of biomass-based rubber. Standards establish uniform criteria for the production, processing, and quality of biomass-based rubber, ensuring consistency and reliability across the industry. These standards can cover various aspects of rubber production, including the sustainability of biomass feed stocks, the efficiency of conversion processes, and the environmental impact of rubber manufacturing.
The International Organization for Standardization (ISO) has developed several standards related to rubber and rubber products, which could be expanded or adapted to include specific criteria for biomass-based rubber. For example, ISO 14000 series standards focus on environmental management, providing guidelines for minimizing environmental impact during production. Similarly, ISO 9000 series standards address quality management systems, ensuring that rubber products meet specified performance and quality requirements.
- Challenges in Certification and Standardization: While certification and standards are essential for promoting sustainable rubber production, there are several challenges to their implementation. One challenge is the complexity and cost of certification, particularly for small-scale producers or those in developing regions. Certification processes can be resource-intensive, requiring significant time, money, and expertise to navigate. This can create barriers to entry for smaller producers who may struggle to meet the stringent requirements of certification programs.
Another challenge is the harmonization of standards across different regions and industries. As biomass-based rubber is a relatively new and evolving field, there is a need for international collaboration to develop consistent and widely accepted standards. This requires coordination between industry stakeholders, governments, and international organizations to ensure that standards are both comprehensive and adaptable to different contexts.
- The Importance of Traceability: Traceability is a key component of certification and standards for sustainable rubber. It involves tracking the origin and movement of biomass feed stocks throughout the supply chain, from cultivation to final product. Traceability systems provide transparency and accountability, helping to ensure that rubber is produced in a way that meets sustainability criteria. Technologies such as block chain and digital tracking can enhance traceability, allowing for real-time monitoring and verification of sustainable practices.
- Future Outlook: As the market for sustainable materials continues to grow, the development of certification and standards for biomass-based rubber will be critical to its success. Industry stakeholders will need to work together to create robust, transparent, and accessible certification schemes that support the adoption of sustainable rubber practices. By establishing clear and consistent standards, the industry can build trust and confidence in biomass-based rubber, paving the way for its widespread adoption as a sustainable alternative to traditional rubber.
Certification and standards are vital tools for ensuring the sustainability of biomass-based rubber. They provide a framework for responsible production practices, promote transparency and accountability, and help to build consumer trust in sustainable rubber products. As the industry evolves, continued efforts to develop and implement certification and standards will be essential for the growth and success of biomass-based rubber in the global market.
12. Regulatory Frameworks Supporting Biomass-Based Rubber
The development and commercialization of biomass-based rubber are heavily influenced by regulatory frameworks that govern the production, use, and disposal of materials. These frameworks play a crucial role in shaping the market for sustainable rubber, providing the necessary legal and policy support to encourage the adoption of environmentally friendly alternatives to traditional rubber. Regulatory frameworks can encompass a wide range of policies, including environmental regulations, incentives for sustainable practices, and standards for product safety and quality.
- Environmental Regulations: Environmental regulations are a key component of the regulatory framework for biomass-based rubber. These regulations aim to minimize the environmental impact of rubber production by setting limits on greenhouse gas emissions, water and energy usage, and waste generation. For example, regulations may require rubber manufacturers to reduce their carbon footprint by sourcing biomass feed stocks that are sustainably grown and processed. Additionally, regulations may mandate the use of environmentally friendly technologies in the production process, such as low-emission conversion methods or the use of renewable energy sources.
In many regions, environmental regulations are increasingly stringent, reflecting growing concerns about climate change and environmental degradation. This trend is creating a favorable environment for the adoption of biomass-based rubber, as it offers a lower environmental impact compared to traditional fossil fuel-based rubber. For instance, the European Union’s Green Deal, which aims to make Europe the first climate-neutral continent by 2050, includes measures to promote the use of sustainable materials, including biomass-based products.
- Incentives for Sustainable Practices: Governments and regulatory bodies can also support the adoption of biomass-based rubber through incentives and subsidies for sustainable practices. These incentives can take various forms, such as tax breaks, grants, or low-interest loans for companies that invest in sustainable technologies or practices. For example, a government might offer financial support to rubber manufacturers that switch from fossil fuel-based feed stocks to biomass, or that invest in new conversion technologies that reduce emissions and energy consumption.
Incentives can also be targeted at the agricultural sector to encourage the cultivation of biomass feed stocks for rubber production. This could include subsidies for farmers who grow guayule, dandelion, or other rubber-producing plants, or who adopt sustainable farming practices that enhance soil health and reduce water usage. By providing financial support, governments can help to offset the higher costs associated with sustainable production methods, making biomass-based rubber more economically viable.
- Product Safety and Quality Standards: Regulatory frameworks also include standards for product safety and quality, which are essential for ensuring that biomass-based rubber meets the necessary performance and safety requirements. These standards can cover a wide range of aspects, including the chemical composition of rubber, its physical properties (such as tensile strength and elasticity), and its safety for use in various applications (such as automotive or medical products).
In some cases, regulatory bodies may develop specific standards for biomass-based rubber to address its unique characteristics and production processes. For example, standards may be established to ensure that biomass-based rubber does not contain harmful chemicals or allergens, particularly in products intended for direct human contact, such as gloves or medical devices or tires. Compliance with these standards is essential for gaining market acceptance and ensuring the safety and reliability of biomass-based rubber products.
- Trade Regulations and Market Access: Trade regulations also play a significant role in shaping the global market for biomass-based rubber. These regulations can include tariffs, import and export restrictions, and trade agreements that affect the flow of rubber and rubber products between countries. For biomass-based rubber to compete effectively on the global market, it must be able to navigate these trade regulations, which can vary widely between regions.
For instance, countries that are major producers of traditional rubber might impose tariffs or other trade barriers to protect their domestic industries from competition by biomass-based alternatives. Conversely, countries that are focused on promoting sustainable development might reduce or eliminate tariffs on biomass-based rubber to encourage its adoption. Additionally, international trade agreements can influence the market dynamics by creating new opportunities for the export of biomass-based rubber to regions with high demand for sustainable materials.
- Waste Management and Recycling Regulations: The regulatory framework for biomass-based rubber also extends to waste management and recycling, which are critical for ensuring the sustainability of rubber products throughout their lifecycle. Regulations may require manufacturers to implement recycling programs or to design products that are easier to recycle. For example, extended producer responsibility (EPR) laws in some regions require manufacturers to take responsibility for the entire lifecycle of their products, including their disposal and recycling.
In the context of biomass-based rubber, recycling regulations can help to close the loop by promoting the recovery and reuse of rubber materials, reducing the need for virgin biomass feed stocks, and minimizing waste. These regulations can also encourage the development of new recycling technologies that are specifically tailored to the unique properties of biomass-based rubber, ensuring that it can be efficiently and effectively recycled at the end of its useful life.
Global Coordination and Harmonization of Regulations: One of the challenges in regulating biomass-based rubber is the need for global coordination and harmonization of regulations. As the production and use of biomass-based rubber expand across different regions, it is important to ensure that regulatory frameworks are aligned to avoid trade barriers and to facilitate the growth of the global market. This requires collaboration between governments, industry stakeholders, and international organizations to develop common standards and regulations that support the sustainable production and use of biomass-based rubber.
For example, the United Nations Environment Programme (UNEP) and other international bodies have been working to develop global guidelines and best practices for sustainable rubber production, which can serve as a foundation for national regulations. Similarly, international trade organizations can play a role in harmonizing trade regulations to ensure that biomass-based rubber can move freely across borders, supporting its adoption on a global scale.
- Abstract: The regulatory framework for biomass-based rubber is a complex and evolving landscape that encompasses environmental regulations, incentives for sustainable practices, product safety and quality standards, trade regulations, and waste management policies. These regulations are essential for supporting the growth and commercialization of biomass-based rubber, ensuring that it can compete effectively with traditional fossil fuel-based rubber while meeting the demands of a sustainable economy.
As the market for biomass-based rubber continues to develop, it will be important for regulatory frameworks to adapt and evolve to address new challenges and opportunities. By providing a supportive and well-coordinated regulatory environment, governments and international organizations can help to drive the adoption of biomass-based rubber, contributing to the global transition toward more sustainable and circular economies.
13. Industry Initiatives and Partnerships for Sustainable Rubber
The transition to biomass-based rubber is not just a matter of technological innovation and regulatory support; it also requires strong industry initiatives and partnerships. These collaborative efforts are essential for driving the development, commercialization, and adoption of sustainable rubber alternatives. By working together, stakeholders across the rubber supply chain—from farmers and researchers to manufacturers and retailers—can overcome the challenges associated with biomass-based rubber and accelerate its integration into the market.
- Industry-Led Initiatives: Various industry-led initiatives have emerged in recent years to promote sustainable rubber production, including biomass-based rubber. These initiatives are often driven by leading companies in the automotive, tire, and consumer goods sectors, which have significant influence over the rubber supply chain. These companies are increasingly recognizing the need to shift toward more sustainable materials and are taking proactive steps to reduce their environmental footprint.
One example is the Global Platform for Sustainable Natural Rubber (GPSNR), an industry-led initiative that brings together stakeholders from across the rubber value chain to promote sustainable practices. GPSNR focuses on improving the sustainability of rubber production through responsible sourcing, environmental protection, and social responsibility. While the platform initially focused on natural rubber, it is increasingly incorporating biomass-based alternatives as part of its broader sustainability goals.
- Public-Private Partnerships: Public-private partnerships (PPPs) are another key driver of innovation in biomass-based rubber. These partnerships bring together government agencies, research institutions, and private companies to collaborate on research and development, pilot projects, and commercialization efforts. By pooling resources and expertise, PPPs can accelerate the development of new technologies and solutions for biomass-based rubber production.
For example, government agencies might provide funding and regulatory support for research projects that explore new biomass feed stocks or conversion technologies, while private companies contribute their technical expertise and market knowledge. Research institutions, in turn, play a crucial role in advancing scientific understanding and developing innovative solutions that can be scaled up for industrial use.
- Collaborative Research and Development: Collaborative research and development (R&D) is essential for overcoming the technical challenges associated with biomass-based rubber. This includes the development of new feed stocks, the optimization of conversion processes, and the improvement of product performance. Collaborative R&D efforts often involve partnerships between universities, research institutions, and industry players, who work together to advance the state of the art in sustainable rubber production.
For instance, research collaborations might focus on identifying and cultivating new biomass sources, such as guayule or dandelion, that can serve as viable alternatives to traditional rubber trees. Other R&D efforts might explore the use of microbial fermentation or other biological processes to convert biomass into rubber, potentially offering more sustainable and efficient production methods.
- Supply Chain Partnerships: Partnerships across the rubber supply chain are also critical for the successful commercialization of biomass-based rubber. These partnerships can help to ensure that biomass feed stocks are sourced sustainably, that conversion processes are optimized for efficiency and sustainability, and that final products meet the necessary quality and performance standards.
For example, tire manufacturers might partner with biomass suppliers to secure a reliable and sustainable source of feed stocks, while working with chemical companies to develop new additives or processing methods that enhance the performance of biomass-based rubber. Retailers, in turn, can play a role by promoting sustainable rubber products to consumers and educating them about the benefits of choosing eco-friendly alternatives.
- Consumer Education and Awareness: Building consumer awareness and demand for biomass-based rubber is another important aspect of industry initiatives. Companies can play a leading role in educating consumers about the environmental benefits of sustainable rubber, as well as the performance characteristics of biomass-based products. This can be achieved through marketing campaigns, product labeling, and corporate sustainability reporting.
Consumer demand is a powerful driver of change, and as awareness of sustainability issues grows, more consumers are likely to seek out products made from sustainable materials. By responding to this demand, companies can differentiate themselves in the market and build brand loyalty among environmentally conscious consumers.
- International Collaboration: Finally, international collaboration is essential for scaling up the production and adoption of biomass-based rubber on a global scale. This includes partnerships between companies in different regions, as well as collaboration with international organizations and NGOs that promote sustainable development. International collaboration can help to share best practices, transfer technology, and create a more cohesive and coordinated approach to sustainable rubber production.
For example, international initiatives such as the Sustainable Natural Rubber Initiative (SNR-i) and the United Nations’ Sustainable Development Goals (SDGs) provide a framework for global cooperation on sustainable rubber production. By aligning their efforts with these initiatives, companies and industry stakeholders can contribute to broader sustainability goals and drive positive change across the rubber industry.
- Abstract: Industry initiatives and partnerships are crucial for advancing the development and commercialization of biomass-based rubber. By working together, stakeholders across the rubber supply chain can overcome the challenges associated with sustainable rubber production, drive innovation, and accelerate the adoption of biomass-based alternatives. Through collaborative efforts, the industry can play a leading role in the transition to a more sustainable and circular economy, helping to reduce the environmental impact of rubber production and meet the growing demand for eco-friendly materials.
14. Public Perception and Awareness of Biomass-Based Rubber
Public perception and awareness are critical factors in the success of biomass-based rubber as a sustainable alternative to traditional rubber. As with any emerging technology or material, how the public perceives the environmental and social benefits of biomass-based rubber can significantly influence its adoption and market growth. Understanding public attitudes, educating consumers, and addressing potential concerns are essential for building widespread support for biomass-based rubber.
- Current Public Awareness Levels: Currently, public awareness of biomass-based rubber is relatively low compared to other sustainable materials, such as recycled plastics or organic cotton. This is partly due to the fact that biomass-based rubber is still a relatively new concept, and its benefits and applications are not yet widely known. Additionally, rubber products are often viewed as commodities, with consumers paying little attention to the materials from which they are made.
However, as environmental concerns become more prominent, consumers are increasingly seeking out sustainable alternatives in all aspects of their lives, including the products they use daily. This trend presents an opportunity to raise awareness about biomass-based rubber and its potential to reduce the environmental impact of rubber production.
- Key Messages for Consumer Education: Educating consumers about the benefits of biomass-based rubber is essential for building public support. Key messages should focus on the environmental advantages of biomass-based rubber, such as its lower greenhouse gas emissions, reduced reliance on fossil fuels, and potential for biodegradability. Additionally, highlighting the fact that biomass-based rubber can be sourced from renewable feed stocks, such as guayule or dandelion, can help consumers understand the sustainability of these products.
It’s also important to communicate the performance benefits of biomass-based rubber, particularly in applications where durability,resilience, and safety are critical, such as in tires or medical gloves. Consumers are often concerned about whether sustainable alternatives can match or exceed the performance of traditional products. Providing clear, evidence-based information about how biomass-based rubber compares to fossil fuel-based rubber in terms of quality and performance can help alleviate these concerns and build confidence in the new material.
- Addressing Misconceptions and Concerns: As with any new technology, there may be misconceptions or concerns about biomass-based rubber that need to be addressed. Some consumers might question the sustainability of the feed stocks used or worry about the environmental impact of large-scale biomass cultivation. Others might be skeptical about the biodegradability or recycling potential of biomass-based rubber products.
To address these concerns, it’s important to provide transparent information about the entire lifecycle of biomass-based rubber, from feedstock sourcing to production and disposal. This includes discussing the sustainability practices employed in growing and harvesting biomass feed stocks, as well as the environmental benefits of using renewable resources over fossil fuels. Additionally, educating consumers about the potential for recycling or composting biomass-based rubber products can help reinforce the message of sustainability.
- Role of Media and Marketing: The media and marketing play a crucial role in shaping public perception and awareness of biomass-based rubber. Positive media coverage of innovative projects and partnerships, such as those involving biomass-based rubber, can help bring the concept to a broader audience and generate interest in sustainable alternatives. Similarly, marketing campaigns that highlight the environmental and performance benefits of biomass-based rubber can help to create a positive image and drive consumer demand.
Brands that incorporate biomass-based rubber into their products have a unique opportunity to position themselves as leaders in sustainability. By clearly communicating the environmental advantages of their products, these brands can attract environmentally conscious consumers and differentiate themselves in a competitive market. Additionally, the use of eco-labels or certifications on products made with biomass-based rubber can further build trust and credibility with consumers.
- Influence of Environmental and Consumer Advocacy Groups: Environmental and consumer advocacy groups can also influence public perception and awareness of biomass-based rubber. These groups often play a key role in raising awareness about environmental issues and promoting sustainable alternatives. By partnering with advocacy organizations, companies involved in the production of biomass-based rubber can leverage their networks and credibility to reach a wider audience and build support for sustainable rubber products.
Advocacy groups can also help to educate the public about the broader environmental and social benefits of sustainable rubber production, such as reducing deforestation, supporting rural economies, and mitigating climate change. This can help to create a positive narrative around biomass-based rubber and encourage consumers to make more sustainable choices.
- Consumer Engagement and Feedback: Engaging directly with consumers and gathering feedback is another important strategy for increasing awareness and acceptance of biomass-based rubber. Companies can use social media, surveys, and other tools to gauge consumer interest, understand their concerns, and respond to questions. By actively listening to consumers and incorporating their feedback into product development and marketing, companies can build stronger relationships with their customers and ensure that biomass-based rubber products meet their needs and expectations.
- Challenges and Opportunities: While there are significant opportunities to raise public awareness and support for biomass-based rubber, there are also challenges to consider. One of the main challenges is overcoming the inertia of established consumer preferences and habits. Many consumers are accustomed to traditional rubber products and may be hesitant to switch to a new material, especially if they perceive it as unproven or experimental.
To overcome this challenge, it’s important to focus on building trust and credibility through transparency, education, and performance validation. Highlighting the real-world applications and successes of biomass-based rubber, such as its use in high-performance tires or medical devices, can help to build consumer confidence and demonstrate that it is a viable and reliable alternative to traditional rubber.
- Abstract: Public perception and awareness are critical to the successful adoption of biomass-based rubber. By educating consumers about the environmental and performance benefits of this sustainable alternative, addressing misconceptions, and engaging with advocacy groups and the media, companies can build support for biomass-based rubber and drive its market growth. As awareness grows, so too will the demand for sustainable rubber products, contributing to a more sustainable and circular economy.
15. Life Cycle Assessment of Biomass-Based Rubber
Life cycle assessment (LCA) is a vital tool for evaluating the environmental impacts of products from cradle to grave, and it plays a crucial role in understanding the sustainability of biomass-based rubber. An LCA examines every stage of a product’s life cycle—from raw material extraction and processing to manufacturing, transportation, use, and end-of-life disposal—allowing for a comprehensive analysis of its environmental footprint. For biomass-based rubber, LCA provides insights into how it compares to traditional fossil fuel-based rubber and identifies areas where further improvements can be made to enhance sustainability.
- Life Cycle Stages in Biomass-Based Rubber: The life cycle of biomass-based rubber begins with the cultivation and harvesting of biomass feed stocks, such as guayule or dandelion. This stage involves the use of land, water, fertilizers, and energy, which can have varying environmental impacts depending on the specific practices employed. The next stage is the conversion of biomass into rubber, which can involve chemical, biological, or thermal processes. This stage also consumes energy and may produce emissions or waste products that need to be managed.
Once the biomass-based rubber is produced, it is manufactured into final products, such as tires or gloves. This manufacturing stage includes processes such as mixing, molding, curing, and finishing, each of which has its own environmental impacts. The finished products are then transported to consumers, where they are used and eventually disposed of or recycled. The end-of-life stage is particularly important for assessing the sustainability of biomass-based rubber, as it determines whether the material can be effectively recycled, composted, or otherwise disposed of in an environmentally friendly manner.
- Comparative LCA of Biomass-Based vs. Fossil Fuel-Based Rubber: One of the key purposes of conducting an LCA for biomass-based rubber is to compare its environmental impacts with those of traditional fossil fuel-based rubber. Such a comparison can highlight the potential benefits of biomass-based rubber, as well as any areas where it may have a higher environmental impact. For example, an LCA might reveal that biomass-based rubber has lower greenhouse gas emissions during production, but higher impacts in terms of land use or water consumption.
In general, LCAs of biomass-based rubber have shown that it can offer significant environmental benefits over fossil fuel-based rubber, particularly in terms of reducing carbon emissions and reliance on non-renewable resources. However, the specific outcomes of an LCA can vary depending on factors such as the type of biomass feedstock used, the conversion process employed, and the geographical location of production. For instance, using guayule grown in arid regions with low water requirements might result in a more favorable LCA outcome than using biomass that requires significant irrigation or fertilizer inputs.
- Environmental Impacts Considered in LCA: An LCA of biomass-based rubber typically considers a range of environmental impacts, including:
- Carbon Footprint: The total greenhouse gas emissions associated with the production, use, and disposal of biomass-based rubber, expressed as CO2 equivalent. This includes emissions from land use changes, energy consumption, and any chemical processes involved in converting biomass into rubber.
- Energy Use: The amount of energy required to produce biomass-based rubber, including the energy needed for cultivation, processing, and manufacturing. This can be expressed as total energy use or as the proportion of renewable vs. non-renewable energy sources.
- Water Use: The amount of water consumed during the production of biomass-based rubber, particularly during the cultivation of biomass feed stocks. Water use is a critical factor in regions where water resources are scarce or under stress.
- Land Use: The amount of land required to grow biomass feed stocks, which can have implications for biodiversity, deforestation, and competition with food production. Sustainable land management practices are essential to minimize negative impacts in this area.
- Toxicity and Pollution: The potential for biomass-based rubber production to release pollutants or toxic substances into the environment, either through the use of chemicals in cultivation or processing, or through emissions from energy use.
- End-of-Life Impact: The environmental impact of disposing of or recycling biomass-based rubber products, including the potential for biodegradation, composting, or other forms of environmentally friendly disposal.
- Challenges in Conducting LCA for Biomass-Based Rubber: Conducting an LCA for biomass-based rubber presents several challenges. One of the main challenges is the variability in feed stocks and production methods, which can lead to different environmental outcomes. Additionally, the availability of data for emerging biomass-based rubber technologies can be limited, making it difficult to conduct a fully comprehensive assessment.
Another challenge is the complexity of evaluating land use impacts, particularly when it comes to assessing the effects on biodiversity and ecosystem services. For example, the conversion of natural habitats to agricultural land for biomass production can have significant ecological consequences that are not always fully captured in an LCA.
- Opportunities for Improvement: Despite these challenges, LCA provides valuable insights that can guide efforts to improve the sustainability of biomass-based rubber. For instance, LCAs can identify “hotspots” in the production process where environmental impacts are particularly high, such as energy use in conversion processes or water consumption in feedstock cultivation. Addressing these hotspots through technological innovation, improved agricultural practices, or more efficient processing methods can lead to significant reductions in the overall environmental impact of biomass-based rubber.
Moreover, LCA can support the development of policies and standards that promote sustainable practices across the rubber supply chain. By providing a scientific basis for evaluating the environmental performance of biomass-based rubber, LCA can help to establish benchmarks for sustainability and drive continuous improvement in the industry.
- Abstract: Life cycle assessment is an essential tool for evaluating the sustainability of biomass-based rubber. By examining the environmental impacts at each stage of the product’s life cycle, LCA provides a comprehensive understanding of how biomass-based rubber compares to traditional rubber and where improvements canbe made. This information is crucial for guiding the development of more sustainable rubber products and ensuring that biomass-based rubber lives up to its potential as a greener alternative to fossil fuel-based rubber.
16. Feedstock Sourcing and Sustainability Considerations
Sourcing sustainable feed stocks is a fundamental aspect of developing biomass-based rubber that genuinely contributes to environmental and economic sustainability. The selection and management of feed stocks not only affect the environmental footprint of the final product but also determine the feasibility of scaling up biomass-based rubber production. Ensuring that these feed stocks are grown and harvested in a manner that minimizes environmental impact, while supporting local economies, is key to the long-term viability of biomass-based rubber.
- Selection of Suitable Feed stocks: The first step in sourcing sustainable feed stocks for biomass-based rubber is the careful selection of plant species that can be grown efficiently and with minimal environmental impact. Guayule and dandelion have emerged as promising candidates due to their resilience and ability to grow in marginal lands, which are not typically suitable for food production. Guayule, for instance, is well-suited to arid regions and requires less water compared to traditional crops like Hevea rubber trees. Dandelion, particularly the Russian variety, is another robust candidate that can be cultivated in temperate climates, reducing the need for intensive agricultural inputs.
- Sustainability in Cultivation: Sustainable cultivation practices are crucial for ensuring that the production of biomass feed stocks does not lead to negative environmental outcomes. This includes adopting practices that reduce water usage, minimize the need for chemical fertilizers and pesticides, and promote soil health. For example, the use of precision Agriculture technologies can help optimize water and nutrient use, reducing waste and environmental contamination. Crop rotation and polyculture practices can also be employed to maintain soil fertility and reduce the incidence of pests and diseases, further lowering the need for chemical inputs.
In addition to these practices, the geographic location of feedstock cultivation is an important consideration. Growing biomass feed stocks in regions that are already experiencing water stress or deforestation pressures can exacerbate environmental challenges. Therefore, it is critical to identify and cultivate biomass feed stocks in areas where their growth will not contribute to these issues. Selecting marginal lands that are unsuitable for food crops can help avoid competition with food production and prevent the displacement of food Agriculture.
- Economic and Social Sustainability: The economic and social aspects of feedstock sourcing are equally important. The cultivation of biomass feed stocks for rubber production has the potential to create economic opportunities, particularly in rural areas where alternative livelihoods may be limited. By providing farmers with a stable income source, biomass cultivation can contribute to rural development and poverty alleviation. However, it is important to ensure that these economic benefits are equitably distributed and that small-scale farmers and local communities are not marginalized in favor of large agribusinesses.
Fair trade practices and equitable profit-sharing arrangements can help ensure that the economic benefits of biomass cultivation are shared by all stakeholders, including farmers, laborers, and local communities. Additionally, supporting local processing facilities can reduce transportation costs and emissions, while creating jobs and stimulating local economies.
- Sustainability Certification and Standards: To ensure that biomass feed stocks are sourced sustainably, certification schemes and sustainability standards play a critical role. These certifications provide assurance to consumers and industry stakeholders that the biomass used in rubber production has been grown and harvested in an environmentally and socially responsible manner. Certifications such as the Forest Stewardship Council (FSC) or Rainforest Alliance, which are well-established in the timber and agricultural industries, could serve as models for developing similar standards for biomass-based rubber.
Sustainability standards can also help address concerns related to land use changes, such as deforestation or the conversion of natural habitats into agricultural land. By adhering to strict criteria for land use, water management, and biodiversity conservation, certified feed stocks can ensure that biomass-based rubber production does not contribute to environmental degradation.
- Challenges in Sustainable Feedstock Sourcing: Despite the potential benefits, there are challenges associated with sourcing sustainable feed stocks for biomass-based rubber. One of the main challenges is the scalability of cultivation practices. While small-scale, sustainable farming practices may be feasible in certain contexts, scaling up production to meet industrial demands can put pressure on land, water, and other resources. This can lead to environmental degradation if not managed carefully.
Additionally, there is the challenge of ensuring consistent quality and supply of feed stocks. Variability in climate conditions, soil quality, and other factors can affect the yield and quality of biomass feed stocks, making it difficult to maintain a stable supply for industrial rubber production. Developing resilient agricultural practices and investing in research to improve crop yields and quality are essential for overcoming these challenges.
- Abstract : Sourcing sustainable feed stocks is a complex but essential aspect of producing biomass-based rubber. By selecting appropriate feed stocks, adopting sustainable cultivation practices, and ensuring economic and social benefits for local communities, the industry can develop a supply chain that supports environmental and economic sustainability. Certification and standards play a critical role in ensuring that these practices are followed and that the biomass used in rubber production contributes positively to the environment and society. Addressing the challenges of scalability and supply consistency will be key to the long-term success of biomass-based rubber as a sustainable alternative to traditional rubber.
17. Technological Advancements in Biomass Conversion Processes
The conversion of biomass into rubber is a technologically complex process that involves transforming raw plant material into a high-performance material suitable for industrial use. Recent technological advancements in biomass conversion processes have been instrumental in making biomass-based rubber a viable alternative to traditional fossil fuel-based rubber. These advancements include improvements in chemical, biological, and thermal conversion methods, which enhance the efficiency, sustainability, and scalability of biomass-based rubber production.
- Chemical Conversion Processes: Chemical conversion processes involve breaking down the complex molecules in biomass into simpler components that can be reassembled into rubber. One of the most significant advancements in this area is the development of more efficient catalysts and chemical pathways that allow for the selective conversion of biomass into isoprene, the key monomer in natural rubber production. These advancements have reduced the energy requirements and environmental impact of the chemical conversion process, making it more sustainable and cost-effective.
In addition to isoprene production, advancements in chemical conversion processes have also led to the development of new types of rubber with enhanced properties. For example, researchers have developed biomass-based elastomers with improved elasticity, durability, and resistance to environmental factors, expanding the potential applications of biomass-based rubber in various industries.
- Biological Conversion Processes: Biological conversion processes leverage the power of microorganisms, such as bacteria or yeast, to convert biomass into rubber precursors. These processes are often more sustainable than chemical methods because they typically operate at lower temperatures and pressures and use renewable feed stocks. Recent advancements in synthetic biology and metabolic engineering have enabled the development of genetically engineered microorganisms that are highly efficient at producing rubber precursors from biomass.
For instance, researchers have engineered strains of bacteria that can convert sugars derived from biomass into isoprene with high yields. These microorganisms can be grown in bioreactors, where they ferment biomass feed stocks to produce rubber precursors. The use of engineered microorganisms has the potential to significantly reduce the environmental impact of rubber production by minimizing the need for harsh chemicals and reducing greenhouse gas emissions.
- Thermal Conversion Processes: Thermal conversion processes, such as pyrolysis and gasification, involve heating biomass to high temperatures in the absence of oxygen to produce bio-oil, syngas, and char. These products can be further processed to produce rubber precursors or used as energy sources in the production process. Recent advancements in thermal conversion technologies have focused on improving the efficiency and selectivity of these processes, as well as developing integrated systems that can simultaneously produce energy and rubber precursors from biomass.
One notable advancement is the development of advanced pyrolysis techniques that allow for the production of high-quality bio-oil with a higher content of desirable chemical compounds. This bio-oil can be upgraded to produce rubber precursors with properties comparable to those derived from fossil fuels. Additionally, advancements in gasification technology have enabled the production of syngas with a higher hydrogen content, which can be used in various chemical processes to produce rubber.
- Hybrid Conversion Processes: Hybrid conversion processes combine elements of chemical, biological, and thermal methods to optimize the conversion of biomass into rubber. For example, a hybrid process might involve the initial thermal conversion of biomass into bio-oil, followed by a biological fermentation step to produce rubber precursors. These hybrid approaches can offer the best of both worlds, combining the efficiency of thermal processes with the sustainability of biological methods.
Recent advancements in hybrid conversion processes have focused on integrating these different methods into a seamless production chain, reducing the need for intermediate steps and lowering the overall energy consumption. By optimizing the combination of different conversion methods, researchers have been able to achieve higher yields of rubber precursors with lower environmental impact.
- Challenges and Opportunities in Biomass Conversion: Despite the significant advancements in biomass conversion processes, there are still challenges that need to be addressed. One of the main challenges is the complexity of biomass as a raw material, which can vary widely in composition depending on the type of feedstock used. This variability can make it difficult to achieve consistent yields and quality in the conversion process.
Another challenge is the scalability of these advanced conversion technologies. While many of these processes have been proven in laboratory settings, scaling them up to industrial levels requires significant investment and infrastructure. Ensuring that these technologies can be scaled up without compromising efficiency or sustainability is crucial for the widespread adoption of biomass-based rubber.
- Abstract: Technological advancements in biomass conversion processes have been pivotal in making biomass-based rubber a viable and sustainable alternative to traditional rubber. Improvements in chemical, biological, and thermal conversion methods have enhanced the efficiency, scalability, and environmental sustainability of biomass-based rubber production. Hybrid conversion processes offer the potential to optimize these methods further, combining their strengths to achieve even better results. However, challenges related to the complexity and scalability of these technologies remain, and continued research and development are needed to overcome these obstacles and fully realize the potential of biomass-based rubber.
18. Applications of Biomass-Based Rubber (Tires, Gloves, etc.)
The versatility of biomass-based rubber opens up a wide array of applications, ranging from traditional products like tires and gloves to innovative uses in emerging industries. As the world shifts towards more sustainable materials, biomass-based rubber is poised to become a critical component in various sectors, offering not only environmental benefits but also competitive performance characteristics.
- Tires and Automotive Components: One of the most significant applications of rubber, whether traditional or biomass-based, is in the manufacturing of tires. The global automotive industry is a massive consumer of rubber, with tires being the primary product. Biomass-based rubber has the potential to revolutionize the tire industry by providing a sustainable alternative to traditional fossil fuel-derived rubber. Tires made from biomass-based rubber can offer comparable performance in terms of durability, traction, and resistance to wear, while significantly reducing the carbon footprint associated with their production.
In addition to tires, biomass-based rubber can be used in various automotive components such as seals, gaskets, and hoses. These components require materials that are flexible, durable, and resistant to a wide range of temperatures and chemicals. The development of biomass-based elastomers with these properties has made it possible to replace traditional rubber in many automotive applications, contributing to the overall sustainability of the vehicle manufacturing process.
- Medical and Health Care Products: The healthcare industry is another significant consumer of rubber, particularly for products like gloves, catheters, and various medical tubing. Biomass-based rubber offers a sustainable alternative for these critical applications. Medical gloves made from biomass-based rubber can provide the necessary elasticity, strength, and barrier protection required in healthcare settings, while also being biodegradable, which is particularly important given the large volume of medical waste generated globally.
In addition to gloves, biomass-based rubber can be used to manufacture other medical devices such as catheters and syringes. The biocompatibility of certain biomass-derived elastomers makes them suitable for contact with human tissues, reducing the risk of allergic reactions and other complications. Moreover, the use of sustainable rubber in healthcare can help reduce the environmental impact of the industry, particularly in terms of waste management and disposal.
- Consumer Goods and Packaging: Beyond industrial and medical applications, biomass-based rubber is finding its way into everyday consumer goods. Products such as footwear, sports equipment, and household items like rubber bands, mats, and grips can all be manufactured using biomass-based rubber. The use of sustainable rubber in these products not only helps reduce dependence on fossil fuels but also appeals to environmentally conscious consumers who are increasingly seeking eco-friendly alternatives.
In the packaging industry, biomass-based rubber can be used to create seals and gaskets for containers, as well as flexible packaging materials that are biodegradable. This is particularly relevant in the context of the growing concern over plastic pollution, as biomass-based rubber offers a sustainable alternative for applications where traditional synthetic rubber or plastics are currently used.
- Electronics and Technology: The electronics industry relies on rubber for various components such as protective casings, insulators, and connectors. Biomass-based rubber can meet the stringent requirements of the electronics industry, including resistance to heat, electricity, and chemicals. The use of biomass-based rubber in electronics not only contributes to the sustainability of the products but also supports the broader goal of reducing the environmental impact of electronic waste.
- Construction and Infrastructure: The construction industry is another area where biomass-based rubber can make a significant impact. Rubber is used in various construction materials, including sealants, gaskets, and vibration dampening systems. Biomass-based rubber offers the same performance characteristics as traditional rubber, with the added benefit of being derived from renewable resources. This can help reduce the carbon footprint of construction projects and support the development of green buildings and infrastructure.
- Emerging Applications: As research and development in biomass-based rubber continue to advance, new applications are emerging in fields such as aerospace, marine, and renewable energy. For example, biomass-based rubber can be used in the manufacturing of components for wind turbines, where flexibility and durability are critical. In the marine industry, sustainable rubber can be used in the production of seals, hoses, and other components that need to withstand harsh environmental conditions.
- Challenges and Opportunities: While the potential applications of biomass-based rubber are vast, there are still challenges to overcome. One of the main challenges is ensuring that biomass-based rubber can consistently meet the performance standards required for different applications. This includes developing formulations that can match or exceed the durability, elasticity, and resistance of traditional rubber.
Another challenge is the cost of production, which can be higher for biomass-based rubber compared to traditional rubber, particularly at the early stages of commercialization. However, as technology advances and economies of scale are achieved, the cost is expected to decrease, making biomass-based rubber more competitive.The applications of biomass-based rubber are diverse, spanning across multiple industries including automotive, healthcare, consumer goods, electronics, and construction. The shift towards sustainable materials is driving the adoption of biomass-based rubber, which offers a viable alternative to traditional rubber without compromising on performance. As research and development continue, the range of applications is expected to expand further, positioning biomass-based rubber as a key material in the transition to a more sustainable future.
19. Future Outlook and Growth Potential for Biomass-Based Rubber
The future of biomass-based rubber is promising, with significant growth potential driven by increasing demand for sustainable materials across various industries. As the world faces mounting environmental challenges, including climate change and resource depletion, the need for alternatives to traditional fossil fuel-based products has never been more urgent. Biomass-based rubber, with its renewable origins and potential for biodegradability, is well-positioned to play a crucial role in this transition.
- Market Trends and Drivers: The growing awareness of environmental issues and the push for sustainable products are major drivers of the biomass-based rubber market. Industries such as automotive, healthcare, and consumer goods are increasingly looking for materials that can help them reduce their carbon footprint and meet the demands of eco-conscious consumers. Biomass-based rubber offers a solution that not only addresses these concerns but also aligns with the broader trend towards circular economy principles, where products are designed to be reused, recycled, or composted at the end of their life cycle.
Regulatory pressures are also playing a significant role in the growth of the biomass-based rubber market. Governments around the world are implementing stricter environmental regulations and setting ambitious targets for reducing greenhouse gas emissions. These regulations are encouraging industries to adopt more sustainable practices and materials, creating a favorable environment for the adoption of biomass-based rubber.
- Technological Innovations and Advancements: The continued development of advanced biomass conversion technologies is critical to the growth of the biomass-based rubber industry. Innovations in chemical, biological, and thermal processes are improving the efficiency, scalability, and cost-effectiveness of biomass-based rubber production. Additionally, ongoing research into new feed stocks, such as guayule and dandelion, is expanding the availability of sustainable raw materials, further supporting the industry’s growth.
Another area of innovation is the development of new formulations and applications for biomass-based rubber. As researchers continue to explore the unique properties of biomass-derived elastomers, new opportunities are emerging in industries such as aerospace, marine, and renewable energy. These innovations are not only expanding the potential market for biomass-based rubber but also enhancing its competitiveness with traditional rubber.
- Challenges to Overcome: Despite the positive outlook, there are challenges that the biomass-based rubber industry must overcome to achieve widespread adoption. One of the primary challenges is cost. Currently, the production of biomass-based rubber is often more expensive than traditional rubber, primarily due to the relatively small scale of production and the early-stage nature of some of the technologies involved. As the industry matures and economies of scale are achieved, it is expected that costs will decrease, making biomass-based rubber more competitive.
Another challenge is the need for infrastructure and supply chain development. The cultivation, processing, and distribution of biomass feed stocks require specialized infrastructure, which may not be readily available in all regions. Building a robust supply chain that can support the large-scale production of biomass-based rubber will be essential for the industry’s growth.
- Sustainability and Environmental Impact: The environmental benefits of biomass-based rubber are one of its most compelling advantages. By using renewable feed stocks and reducing reliance on fossil fuels, biomass-based rubber can significantly lower greenhouse gas emissions associated with rubber production. Additionally, the potential for biodegradability and recyclability of biomass-based rubber products can contribute to reducing waste and supporting circular economy goals.
However, it is important to ensure that the production of biomass-based rubber does not lead to unintended environmental consequences, such as deforestation or the overuse of water and other resources. Sustainable sourcing of feed stocks and adherence to environmental standards and certifications will be crucial to maintaining the environmental integrity of biomass-based rubber.
- Global Market Potential: The global market for biomass-based rubber is expected to grow significantly in the coming years, driven by increasing demand for sustainable materials in developed and emerging economies alike. In regions such as Europe and North America, where environmental regulations are particularly stringent, the adoption of biomass-based rubber is likely to be strong. In emerging markets, the growth of industries such as automotive and construction, combined with increasing environmental awareness, presents a significant opportunity for biomass-based rubber.
The expansion of the global market will also depend on the industry’s ability to overcome the challenges of cost and infrastructure and to demonstrate the performance and reliability of biomass-based rubber in various applications. Strategic partnerships, investment in research and development, and supportive government policies will all play a role in realizing the full potential of biomass-based rubber.
- Abstract: The future outlook for biomass-based rubber is bright, with strong growth potential driven by market trends, technological advancements, and increasing demand for sustainable materials. While there are challenges to overcome, including cost and infrastructure development, the environmental benefits and wide range of applications for biomass-based rubber position it as a key material in the transition to a more sustainable and circular economy. As the industry continues to innovate and scale up production, biomass-based rubber is likely to become an increasingly important alternative to traditional rubber, contributing to amore sustainable future.
20. Biomass-Based Rubber as a Promising Sustainable Alternative
The development and adoption of biomass-based rubber represent a significant step forward in the quest for sustainable materials. As the global demand for rubber continues to grow, driven by industries such as automotive, healthcare, and consumer goods, the need for alternatives to traditional fossil fuel-based rubber becomes increasingly urgent. Biomass-based rubber, derived from renewable feed stocks such as guayule, dandelion, and other plant-based sources, offers a viable and environmentally friendly solution to this challenge.
- Environmental and Economic Benefits: One of the most compelling advantages of biomass-based rubber is its potential to reduce the environmental impact of rubber production. By utilizing renewable biomass feed stocks, the production of biomass-based rubber can significantly lower greenhouse gas emissions and reduce reliance on finite fossil resources. Additionally, the potential for biodegradability and recyclability of biomass-based rubber products aligns with the principles of the circular economy, offering a more sustainable approach to resource management.
From an economic perspective, the growth of the biomass-based rubber industry presents new opportunities for innovation, job creation, and economic development. As technological advancements continue to improve the efficiency and scalability of biomass conversion processes, the cost of producing biomass-based rubber is expected to decrease, making it increasingly competitive with traditional rubber. Moreover, the development of sustainable supply chains for biomass feed stocks can support rural economies and promote the sustainable use of agricultural resources.
- Challenges and the Path Forward: While the promise of biomass-based rubber is clear, there are challenges that must be addressed to achieve widespread adoption. These include the current cost of production, the need for specialized infrastructure and supply chains, and the necessity of ensuring that the production of biomass feed stocks is sustainable and does not lead to unintended environmental consequences.
To overcome these challenges, continued investment in research and development is essential. Innovations in biomass conversion technologies, the development of new formulations and applications for biomass-based rubber, and the exploration of new feed stocks are all critical to advancing the industry. Additionally, supportive government policies and regulations, along with industry collaboration and partnerships, will play a key role in fostering the growth of the biomass-based rubber market.
- Sustainable Future for Rubber: The transition to biomass-based rubber represents a significant opportunity to reduce the environmental impact of one of the world’s most widely used materials. By embracing renewable feed stocks and sustainable production practices, the rubber industry can contribute to global efforts to combat climate change, reduce waste, and promote the sustainable use of natural resources.
As the world moves towards a more sustainable future, biomass-based rubber is poised to become an increasingly important alternative to traditional rubber. Its potential to meet the performance requirements of various industries while offering environmental and economic benefits makes it a promising solution for the challenges of the 21st century. With continued innovation, collaboration, and commitment to sustainability, biomass-based rubber can play a key role in the transition to a more sustainable and resilient global economy.
The journey from biomass to rubber is more than just a technological advancement; it is a transformative shift towards a more sustainable and responsible approach to material production. As industries and consumers alike recognize the importance of sustainability, biomass-based rubber will likely emerge as a cornerstone of the new, greener economy, providing a renewable, biodegradable, and eco-friendly alternative to traditional rubber that meets the demands of a rapidly changing world.